In 1908, Henry Ford introduced the Model T, a car that would change the world. However, it wasn’t just the car itself that transformed history—it was how Ford made it. By 1913, Ford had developed the moving assembly line, a revolutionary manufacturing process that dramatically cut production time. The assembly line reduced the time to build a car from more than 12 hours to just one hour and 33 minutes, making automobiles affordable for average Americans for the first time.

Ford’s innovation went beyond faster production. He combined interchangeable parts with subdivided labor and fluid movement of materials. Instead of workers moving around to build a car, the car moved to the workers. This approach created specialized jobs that required less training and increased efficiency.
Key Takeaways
- Henry Ford’s moving assembly line revolutionized manufacturing by reducing car production time from 12 hours to 93 minutes.
- The Model T became affordable for middle-class Americans, transforming personal transportation and American society.
- Ford’s production methods created the foundation for modern mass manufacturing techniques used across industries worldwide.
The Early Years of Henry Ford

Henry Ford’s journey from a farm boy to automotive pioneer laid the foundation for his revolutionary impact on manufacturing and transportation. His early experiments with gasoline engines, creation of the Quadricycle, and founding of Ford Motor Company set the stage for his later achievements.
From Farm to Automotive Pioneer
Henry Ford was born on July 30, 1863, on a farm in Dearborn, Michigan. From an early age, he showed a natural talent for mechanics, often dismantling and reassembling watches and other machinery.
In 1879, at age 16, Ford left the farm to work as an apprentice machinist in Detroit. This move marked his first step toward his future in the automotive industry.
By 1891, Ford had become an engineer at the Edison Illuminating Company. This position provided him with income and time to experiment with gasoline engines. His work at Edison was crucial, as it gave him technical knowledge and resources for his automotive dreams.
Thomas Edison himself became a supporter of Ford’s ideas, encouraging him to pursue his interest in self-propelled vehicles.
Developing the Quadricycle
In 1896, Ford completed his first successful automotive project—the Quadricycle. This vehicle featured a simple frame with four bicycle wheels and was powered by a four-horsepower engine.
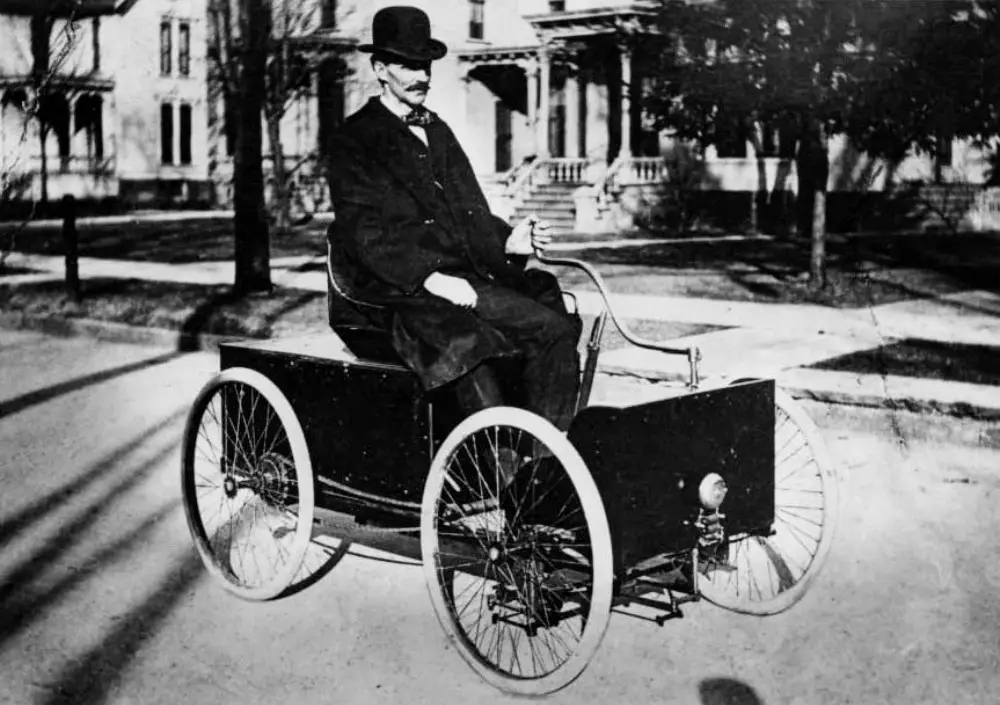
The Quadricycle was quite basic by modern standards. It had no reverse gear, lacked a proper brake system, and could reach speeds of about 20 mph. Despite its limitations, it represented Ford’s first functioning automobile.
Ford tested his invention on the streets of Detroit in the early morning of June 4, 1896. The vehicle was too wide to exit his workshop, so Ford took an ax to the brick wall to make space.
This first vehicle laid the groundwork for Ford’s future designs. He sold the Quadricycle for $200, using the money to fund his next automotive ventures.
The Establishment of Ford Motor Company
After two failed business attempts, Ford formed the Ford Motor Company on June 16, 1903, with $28,000 in capital from twelve investors. The company began in a converted factory in Detroit.
The first Ford automobile, the Model A, was sold in July 1903. The company sold 1,700 Model A cars in its first year, establishing Ford as a viable manufacturer in the competitive early automobile market.
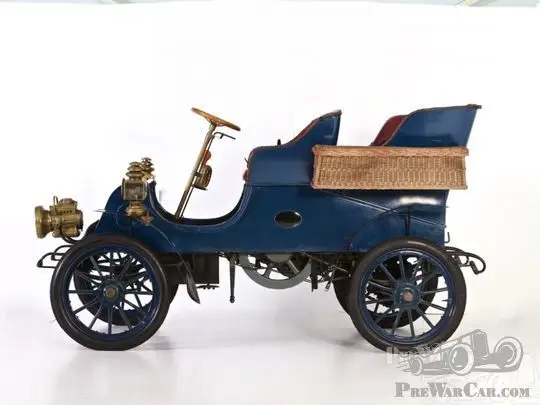
Early Ford Motor Company faced numerous challenges, including patent battles with the Association of Licensed Automobile Manufacturers. Ford fought and won these legal battles, allowing his company to grow.
By 1908, Ford had refined his vision of creating an affordable, reliable car for the average American. This led to the development of the Model T, which would transform manufacturing and make Ford a household name worldwide.
Innovations in Manufacturing

Henry Ford’s most significant contribution to the automotive industry came through his revolutionary manufacturing techniques. These innovations transformed not just how cars were built, but also established new standards for industrial production worldwide.
The Moving Assembly Line
Ford introduced the moving assembly line in his Highland Park factory in 1913. This system completely changed how cars were manufactured. Instead of workers moving around to build a car, the car moved to them.
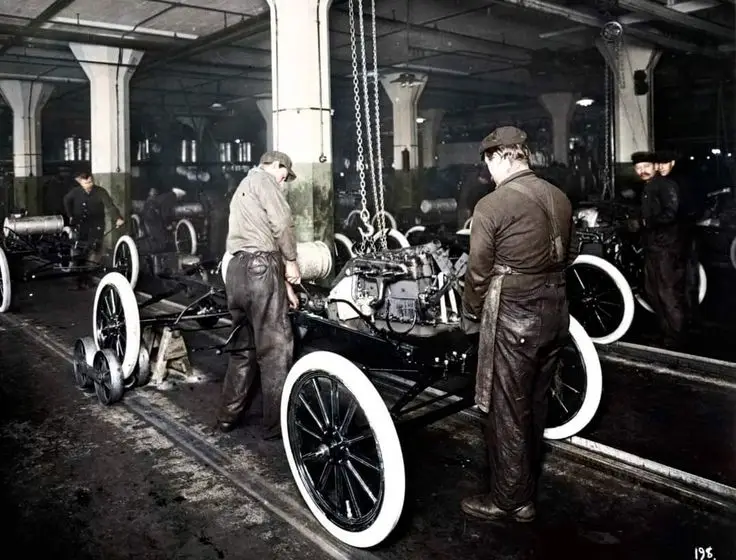
The innovation combined three key principles: interchangeable parts, subdivided labor, and continuous flow of materials. Each worker performed a single, specific task repeatedly as the vehicle chassis moved along the line.
This approach eliminated wasted motion and standardized the production process. Workers no longer needed to be skilled in multiple aspects of automobile construction.
The assembly line concept wasn’t entirely new, but Ford perfected it for complex manufacturing. He took inspiration from other industries like meatpacking and adapted it to car production at an unprecedented scale.
Reducing Production Time
Before the assembly line, building a single Model T took skilled workers about 12 hours to complete. Ford’s new system dramatically cut this time to under three hours per vehicle.
The efficiency gains were staggering. By 1914, Ford could produce a complete chassis every 93 minutes. This was a revolutionary improvement in manufacturing speed.
This reduction in production time allowed Ford to make more cars with fewer labor hours. The cost savings were then passed on to consumers, making automobiles affordable for average Americans.
With increased production capacity, Ford’s factories could meet growing demand. Annual production jumped from 10,000 units in 1908 to over 2 million by the early 1920s.
Advent of the $5 Workday
In 1914, Ford made another bold move by introducing the “$5 workday” – doubling the average factory wage. This decision shocked the business world but proved strategically brilliant.
The higher wages reduced employee turnover significantly. Before this change, Ford had to hire 963 workers for every 100 jobs due to high turnover. The $5 wage helped stabilize his workforce.
Better pay also meant workers could afford the very products they built. Many Ford employees became Model T owners, expanding the market for Ford’s vehicles.
The wage increase came with conditions. Workers had to maintain certain lifestyle standards and could be subject to home visits by the company’s “Sociological Department” to ensure compliance with Ford’s values.
This pay innovation transformed industrial labor relations and helped create a new American middle class with purchasing power to fuel economic growth.
The Model T: Vehicle of the Masses

The Ford Model T transformed transportation by making automobiles accessible to ordinary Americans. It combined innovative design, manufacturing efficiency, and affordability in ways that changed society forever.
Designing for the Average Consumer
Henry Ford had a clear vision when designing the Model T in 1908. He famously declared, “I will build a car for the great multitude.” Unlike luxury vehicles of the time, the Model T was created to be:
- Affordable for middle-class families
- Simple to operate and maintain
- Durable enough for rough rural roads
- Practical for everyday use
The Model T initially sold for $850, but Ford’s manufacturing innovations eventually dropped the price to $260 by 1925. This dramatic price reduction made car ownership possible for millions of Americans.
The vehicle’s high ground clearance and sturdy construction made it ideal for America’s largely unpaved roads. Its simplicity allowed owners to make most repairs themselves with basic tools.
Implementing Interchangeable Parts
The Model T revolutionized automobile manufacturing through standardized, interchangeable parts. Before this approach, each car was essentially handmade with unique components.
Ford’s system ensured that:
- Every part was manufactured to precise specifications
- Components could be swapped between vehicles
- Assembly workers needed less specialized training
- Production speed increased dramatically
This standardization allowed for rapid repairs and simplified manufacturing processes. It reduced costs while maintaining consistent quality across all vehicles.
The precision manufacturing also meant spare parts could be produced in bulk and distributed widely. Owners could replace broken components easily, extending their vehicles’ lifespans.
Spearheading Mass Production
The Model T became the first truly mass-produced vehicle in history. The moving assembly line introduced in 1913 transformed manufacturing forever.
Before the assembly line, workers built one car at a time. Ford’s innovation:
- Reduced assembly time from 12.5 hours to just 93 minutes
- Enabled workers to specialize in single tasks
- Created continuous workflow through the factory
- Dramatically increased production volume
This efficiency allowed Ford to produce over 15 million Model Ts between 1908 and 1927. The car became so common that by the 1920s, more than half of all automobiles worldwide were Model Ts.
Ford’s $5 workday policy ensured his employees could afford the very products they built, creating a new consumer class and economic model that would define American manufacturing for decades.
Fordism and Its Impact on Society

Fordism transformed not only manufacturing but also society as a whole through its revolutionary approach to production. The system created ripple effects that changed employment practices and set global standards for decades to come.
Shaping Industrial Employment
Henry Ford’s approach to labor relations marked a significant shift in industrial employment. In 1914, he introduced the five-dollar workday, which was double the average wage at the time. This bold move served multiple purposes.
Ford believed higher wages would reduce worker turnover and increase loyalty. The improved pay allowed workers to afford the very products they built, creating a new consumer class of factory employees.
The assembly line system also changed the nature of work itself. Jobs became more specialized and repetitive, requiring less skilled labor but demanding greater efficiency. Workers performed specific tasks rather than crafting entire products.
This transformation created a new industrial middle class but also faced criticism for making work monotonous and treating workers like extensions of the machinery they operated.
Influencing Global Manufacturing Practices
Fordism as an industrial paradigm spread far beyond Detroit, reshaping manufacturing worldwide. Its core principles of standardization, efficiency, and mass production became the dominant manufacturing model for much of the 20th century.
The assembly line approach dramatically cut production time. Ford’s methods reduced automobile assembly time from over 12 hours to just 90 minutes, a revolution in manufacturing efficiency.
Global industries adopted these techniques across sectors from appliances to electronics. Japan’s Toyota eventually built upon Ford’s ideas to create lean manufacturing, showing Fordism’s continuing influence and evolution.
Fordism’s most lasting impact may be how it changed consumption patterns. By making products affordable through mass production, it created the modern consumer economy where middle-class families could purchase previously luxury items.
Beyond Automobiles: Diversifying the Industry

Henry Ford’s vision extended far beyond the production of affordable cars. His innovations and manufacturing techniques soon spread to other industries and products, showing the versatility of his assembly line concept.
From Racing Cars to Bombers
Ford’s interest in racing began early in his career as a way to prove his engineering skills. In 1901, he built and raced a car that beat Alexander Winton, a leading automobile manufacturer of the time. This victory helped Ford attract investors for his new company.
The Model B and Model F were early Ford racing models that showcased the company’s technical abilities. These specialty vehicles demonstrated that Ford’s production methods could be adapted for different types of automobiles beyond the basic Model T.
During World War II, Ford’s manufacturing expertise proved crucial to the American war effort. The company converted its automobile factories to produce military equipment including jeeps, tanks, and armored cars.
Most impressively, Ford built the massive Willow Run Plant near Detroit specifically to manufacture B-24 Liberator bombers. Using assembly line techniques, the factory eventually produced one bomber per hour—an unprecedented rate for such complex machines.
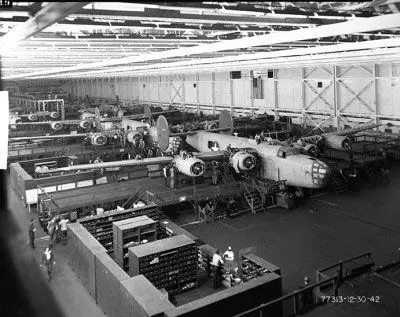
An Advent into Aviation and Beyond
Ford’s interest in aviation began in the 1920s when he established the Ford Airplane Company. Though this venture didn’t last long, it demonstrated his belief that airplane manufacturing could benefit from the same mass production techniques used for automobiles.
In 1925, Ford purchased the Stout Metal Airplane Company and developed the Ford Trimotor, an all-metal aircraft nicknamed the “Tin Goose.” This reliable plane helped establish commercial passenger service in America and showed how assembly line methods could be applied to aircraft production.
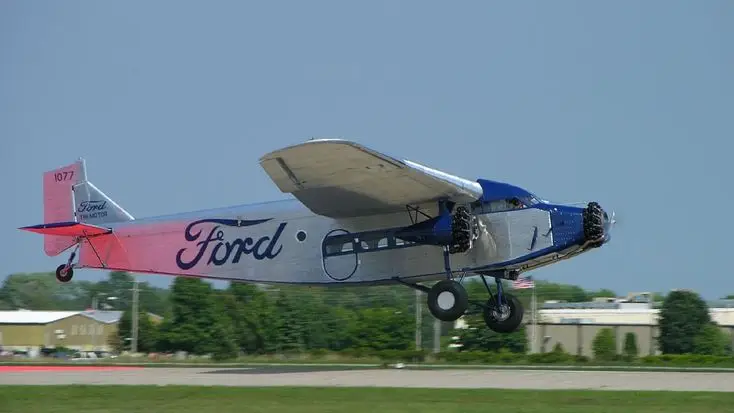
Ford’s manufacturing principles extended to other industries as well:
- Agriculture: Ford tractors (Fordson) revolutionized farming with affordable mechanization
- Shipping: Ford applied assembly techniques to build submarine chasers and cargo ships
- Home appliances: The company briefly produced electrical generators for rural homes
Ford’s willingness to adapt his assembly line concept to various products demonstrated the versatility of his manufacturing approach. This diversification showed how industrial techniques developed for automobiles could transform production across multiple sectors.
Evolution of the Ford Motor Company

Ford Motor Company grew from a small operation into one of the world’s largest automakers through innovation and adaptation. Its journey spans over a century of automotive milestones and cultural impact.
The Growth into an Automotive Giant
Henry Ford established the Ford Motor Company in 1903 with just $28,000 from 12 investors. The company’s early breakthrough came with the Model T in 1908, which revolutionized personal transportation in America.
By 1913, Ford introduced the moving assembly line, dramatically reducing production time from 12.5 hours to just 93 minutes per vehicle. This innovation allowed the company to produce cars faster and cheaper than competitors.
Ford expanded globally in the 1920s and 1930s, establishing manufacturing plants across Europe and Asia. During World War II, the company shifted to producing military vehicles and equipment, demonstrating its industrial might.
The post-war era brought iconic vehicles like the Thunderbird (1955) and Mustang (1964), cementing Ford’s position as an automotive powerhouse with diverse vehicle offerings across multiple segments.
Celebrating the Centennial: Ford Fans and Legacy
Ford’s 100th anniversary in 2003 brought tremendous celebration among Ford fans worldwide. Enthusiasts organized rallies, car shows, and special events to honor the brand’s legacy.
The company marked its centennial by releasing commemorative editions of popular models. These limited-edition vehicles became instant collectibles among dedicated Ford enthusiasts.
Ford’s impact extends beyond automobiles. The $5 workday introduced in 1914 helped create America’s middle class, while the company’s manufacturing techniques transformed global industry.
Ford’s legacy includes both technological innovation and cultural influence. Ford memorabilia, from vintage signs to model cars, remains highly sought after by collectors passionate about the brand’s history.
Today, Ford continues evolving with electric vehicles and digital technology while maintaining connections to its rich heritage that resonates with generations of loyal customers.
Modern Manufacturing Advancements

Ford’s revolutionary assembly line has evolved dramatically with technological innovation transforming automotive production. Today’s manufacturing capabilities blend human expertise with cutting-edge technologies.
Integration of Robotics and Advanced Machines
Modern car factories now employ sophisticated robotic systems that handle everything from welding to painting with precision impossible for human hands. These robots work alongside humans in collaborative environments, taking on dangerous or repetitive tasks.
3D printing has revolutionized prototyping, allowing manufacturers to create complex parts in hours instead of days. This technology enables rapid testing of new designs without expensive tooling changes.
Virtual manufacturing simulations let engineers test production processes before implementing them on the factory floor. These digital twins help identify potential problems early, saving time and resources.
Automated guided vehicles (AGVs) now transport parts throughout factories, replacing the fixed conveyor systems that Henry Ford pioneered. This flexibility allows production lines to be reconfigured quickly for different models.
Leading in Advanced Manufacturing Techniques
Modern assembly lines can now produce a vehicle in about 24 seconds, compared to the 90 minutes achieved by Ford’s original moving assembly line. This incredible efficiency comes from integrated computer systems that coordinate every aspect of production.
Smart factories use IoT sensors to monitor equipment health, predicting maintenance needs before breakdowns occur. This predictive approach minimizes costly downtime and ensures consistent quality.
Flexible manufacturing systems allow multiple vehicle models to be built on the same line. Unlike Ford’s original single-model approach, today’s factories can switch between different vehicles with minimal changeover time.
Artificial intelligence optimizes production scheduling and resource allocation, making decisions based on real-time data from thousands of inputs across the factory. This maximizes efficiency while maintaining high quality standards.
Innovative Production Processes

Henry Ford’s revolutionary manufacturing methods transformed the automotive industry by prioritizing efficiency and standardization. His innovations continue to influence modern production techniques at Ford and beyond.
The Implementation of Flexible Manufacturing
Ford’s assembly line concept has evolved dramatically into flexible manufacturing systems that adapt to changing consumer demands. Unlike the original Model T production, which made identical vehicles, today’s Ford plants can produce multiple models on the same line.
Flexible manufacturing allows quick adjustments to production capabilities based on market preferences. Modern Ford facilities operate as virtual factories where computer simulations test processes before physical implementation.
The company’s Ford Freeform Fabrication Technology creates prototype stamping molds in days rather than months. This advancement significantly reduces development time and costs while allowing rapid design modifications.
Workers benefit from improved ergonomic standards throughout production areas. These adjustments reduce physical strain and increase efficiency while maintaining high quality standards.
Improving Quality with High-Tech Systems
Ford revolutionized quality control through advanced technology integration. The Dirt Detection System uses high-resolution cameras to identify surface imperfections invisible to the human eye.
This technology scans vehicle bodies during production, automatically flagging areas needing attention. The system can detect particles smaller than a grain of salt, ensuring flawless paint finishes.
Ford’s manufacturing innovations reduced assembly time per vehicle from over 12 hours to fewer than three hours. Today’s advanced processes continue this efficiency tradition while maintaining exceptional quality.
Automated inspection robots verify tolerances to fractions of a millimeter. These systems ensure consistent quality across all vehicles while collecting data to further improve manufacturing processes.
Henry Ford’s Legacy and Contributions

Henry Ford transformed manufacturing forever with his groundbreaking ideas that made cars affordable for average Americans. His innovations extended far beyond just creating vehicles to completely reshaping how products are made.
Changing the Face of Transportation
Ford didn’t invent the automobile, but he revolutionized how cars were built and sold. His most famous achievement was the Model T, introduced in 1908, which became the first car many Americans could afford.
The true genius of Ford’s approach was his development of the moving assembly line, implemented in 1913. This innovation dramatically cut production time by bringing the work to the workers instead of workers moving around the factory.
Before the assembly line, it took 12 hours to build one car. After implementing his system, Ford could produce a Model T in just 24 seconds. This efficiency led to lower prices, making cars accessible to the middle class for the first time.
Influence on the Modern Industrial Landscape
Ford’s manufacturing techniques permanently changed how products are made worldwide. His assembly line concept became the standard for industrial practice throughout the first half of the 20th century.
He introduced the $5 workday in 1914, doubling the average factory wage. This bold move helped create a new consumer class while reducing employee turnover.
Ford’s emphasis on standardization and efficiency inspired countless other industries beyond automotive manufacturing. His principles of mass production created the blueprint for modern factories.
His business model proved that making affordable products for many consumers could be more profitable than selling expensive items to a few. This approach helped fuel America’s consumer economy and middle-class growth throughout the 20th century.
Frequently Asked Questions

Henry Ford’s revolutionary manufacturing approach transformed not just the automobile industry but also manufacturing processes worldwide. His innovative ideas changed how products were made and had far-reaching effects on society and economics.
What innovation by Henry Ford revolutionized manufacturing?
Henry Ford’s most revolutionary innovation was the moving assembly line, introduced in 1913. This system brought the work to the workers rather than having workers move around to complete tasks.
The assembly line allowed for efficient division of labor where each worker performed a specific task as the vehicle moved along the production line. This approach dramatically reduced the time needed to build each automobile.
Ford combined the concepts of interchangeable parts with subdivided labor and the fluid movement of materials to create this manufacturing breakthrough.
What were the primary effects of the assembly line on the automobile industry?
The assembly line made cars significantly cheaper to produce. Production time for a single vehicle dropped from 12.5 hours to just 93 minutes.
This efficiency led to lower prices, making automobiles affordable for middle-class Americans for the first time. The Model T’s price fell from $850 in 1908 to under $300 by the 1920s.
The assembly line also standardized automobile production methods, forcing competitors to adopt similar techniques to remain competitive in the market.
How did the introduction of the moving assembly line impact industrial productivity?
Industrial productivity skyrocketed after the implementation of the assembly line. Ford’s factories could produce cars at unprecedented rates, with much greater consistency and quality control.
Worker productivity increased dramatically as each person mastered their specific task rather than needing to know the entire manufacturing process. This specialization led to greater efficiency.
The assembly line set the standard for worldwide industrial practice throughout the first half of the 20th century, establishing new benchmarks for production speed and efficiency.
In what ways did Henry Ford’s manufacturing techniques influence modern society?
Ford’s manufacturing techniques helped create the modern consumer economy by making products more affordable for the average person. This accessibility transformed American society.
His production methods also changed labor practices. Ford famously introduced the $5 workday in 1914, more than doubling the typical wage and establishing the concept of paying workers enough to afford the products they made.
These manufacturing innovations helped accelerate America’s shift from an agricultural society to an industrial powerhouse, changing where and how people lived and worked.
What were the most significant changes in car production due to the assembly line?
The most significant change was the dramatic reduction in production time and costs. Cars became standardized products rather than custom-built luxury items.
Quality control improved as each worker became highly skilled at their specific task, reducing errors and inconsistencies in the final product.
The assembly line also allowed for faster and cheaper car production, making automobiles accessible to a much broader segment of the population than ever before.
How did the assembly line concept extend beyond automobile manufacturing?
The assembly line concept quickly spread to other manufacturing sectors, including appliances, electronics, and consumer goods. Any product with multiple components benefited from this approach.
Food processing and packaging industries adopted similar principles, revolutionizing how Americans shopped for and consumed food products.
Even service industries eventually incorporated elements of Ford’s system, with specialized workers handling specific aspects of customer service in sequence—a concept still visible in modern fast-food operations and customer service processes.